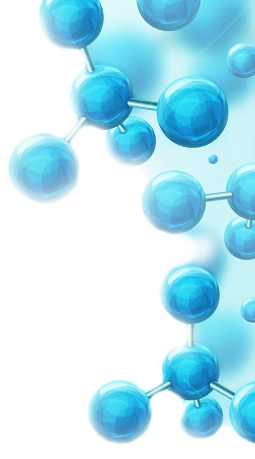
At the present time, welding with one-component gases is outdated. The use of multicomponent gas mixtures based on argon (Ar) has become the modern stage of increasing the efficiency in the manufacture of welded metal structures. By changing the composition of the gas mixture, it is possible within certain limits to change the properties of the metal, the weld, and the welded joint as a whole. The advantages of such a welding process are that an inkjet and controlled process of transfer of the electrode metal is possible. These changes in the welding arc are an effective way to control its technological characteristics, such as:
- performance
- the magnitude of the loss of the electrode metal to spray,
- the form,
- mechanical properties of the weld metal,
- the amount of penetration of the base metal.
The percentage of a gas in the mixture is taken based on the thickness of the metal being welded, the degree of doping and the requirements for welded joints, depending on the operating conditions of the product. The areas of application of various gas mixtures in consumable electrode welding and welding modes are given in the tables below. These mixtures are tested in practice, which allows us to recommend their use to obtain high-quality welded joints.
Welding gas mixtures and recommended areas of uses
Component composition gas mixture | nominal value of the content of components, % | Welder materials | Application area |
CO2 Ar | 5 – 20% 80 – 95% | Carbon and alloy structural steels | Drop or jet transfer of electrode metal. Arc stability. Welding of metals of a wide range of thicknesses. |
CO2 O2 Ar | 6.0% 2.0% 92% | Carbon and alloy structural steels | Drop or jet transfer of electrode metal. Ideal for the welding of metals of a small thicknesses. |
CO2 O2 He | 1.5% 13.5% 85% | Carbon and alloy structural steels | Pulsating arc welding. It gives excellent clean seams with smooth profile with little surface oxidation. Ideal for thin materials, where high welding speed give a low level of material deformation. |
CO2 O2 He | 2% 43% 55% | Carbon and alloy structural steels | Low level of reinforcement of weld metal and heat-affected zone. Suitable for welding a wide range of metal thicknesses. |
CO2 O2 He | 2% 60% 38% | Non-ferous metal and their alloys. Medium and high alloy steels. | Drop or jet transfer of electrode metal. It gives stability to the arc, which ensures a low level of splashing and reduces the appearance of weld defects. |
He Ar | 70% 30% | Non-ferous metal and their alloys. Medium and high alloy steels. | Inert gas mixture. Gives more effective heating, than pure argon. Increases welding speed. Provides deep penetration, low porosity and a even surface of a weld. |
He Ar | 50% 50% | Non-ferous metal and their alloys. Medium and high alloy steels. | Inert, the most versatile gas mixture for welding materials of any thickness. |
He Ar | 70% 30% | Non-ferous metal and their alloys. Medium and high alloy steels. | Inert blend, used for thick materials, which can significantly increase the welding speed, reduce porosity and reduce the need for preheating. Gives a smooth weld with deeper penetration and fewer defects. |
Recommended protective gas mixtures and welding conditions depending on the type and thickness of the material (consumable electrode welding)
Materials
| Thinkness, mm | Recommended mixture, % | Diameter welding wire, мм | Speed welding, мм / хв | І А | U B | Wire feed speed, m / min | Gas conumption, L / min |
Carbon structural steels | 1 | CO2 6,0% O2 2,0% Ar 92,0% | 0,8 | 350-600 | 45-65 | 14-15 | 3,5-4,0 | 12 |
1,6 | 0,8 | 400-600 | 70-80 | 15-16 | 4,0-5,3 | 14 | ||
3 | CO2 6,0%O2 2,0% Ar 92,0% | 1,0 | 280-520 | 120-160 | 17-9 | 4,0-5,2 | 15 | |
6 | 1,0 | 300-450 | 140-160 | 17-18 | 4,0-5,0 | 15 | ||
6 | 1,2 | 420-530 | 250-270 | 26-28 | 6,6-7,3 | 15 | ||
10 | 1,2 | 300-450 | 140-160 | 17-18 | 3,2-4,0 | 15 | ||
10 | CO2 18,0% Ar 82,0% | 1,2 | 400-480 | 270-310 | 26-28 | 7,0-7,8 | 16 | |
>10,0 | 1,2 | 300-450 | 140-160 | 17-18 | 3,2-4,0 | 15 | ||
>10,0 | CO2 6,0% O2 2,0% Ar 92,0% | 1,2 | 370-440 | 290-330 | 28-31 | 10,0-12,0 | 17 | |
Alloyed steel | 1,6 | CO2 1,5% Ar 13,5% He 85,0% | 0,8 | 410-600 | 70-85 | 19-20 | 6,5-7,1 | 12 |
3 | CO2 2,0% Ar 43,0% He 55,0% | 1,0 | 400-600 | 100-125 | 16-19 | 5,0-6,0 | 13 | |
5 | 1,0 | 280-520 | 120-150 | 16-19 | 4,0-6,0 | 14 | ||
6 | 1,2 | 500-650 | 220-250 | 25-29 | 7,0-9,0 | 14 | ||
10 | CO2 2,0%Ar 60,0% He 38,0% | 1,2 | 250-450 | 120-150 | 16-19 | 4,0-6,0 | 14 | |
10 | 1,2 | 450-600 | 260-280 | 26-30 | 8,0-9,5 | 14 | ||
>10,0 | 1,2 | 220-400 | 120-150 | 16-19 | 4,0-6,0 | 15 | ||
>10,0 | 1,2 | 400-600 | 270-310 | 28-31 | 9,0-10,5 | 15 | ||
Aluminium and its alloys | 1,6 | He 30,0% Ar 70,0% | 1,0 | 450-600 | 70-100 | 17-18 | 4,0-6,0 | 14 |
3 | 1,2 | 500-700 | 105-120 | 17-20 | 5,0-7,0 | 14 | ||
6 | 1,2 | 450-600 | 120-140 | 20-24 | 6,5-8,5 | 14 | ||
6 | He 50,0% Ar 50,0% | 1,2 | 550-800 | 160-200 | 27-30 | 8,0-10,0 | 14 | |
10 | 1,2 | 450-600 | 120-140 | 20-24 | 6,5-8,5 | 16 | ||
10 | 1,6 | 500-700 | 240-300 | 29-32 | 7,0-9,0 | 16 | ||
>10,0 | 1,2-1,6 | 400-500 | 130-200 | 20-26 | 6,5-80 | 18 | ||
>10,0 | He 70,0% Ar 30,0% | 12,-1,6 | 450-700 | 300-500 | 32-40 | 9,0-14,0 | 18 |